PLA vs. ABS
- Maryanne Olson
- Sep 21, 2016
- 3 min read

Of all the different types of material used in FDM/FFF printing, the two most popular materials are PLA and ABS. Both of these materials are types of thermoplastics. Thermoplastics are plastics that are hard and solid when cooled and moldable and soft when heated. Thermoplastics are common in society and make up most of the plastic objects that we are familiar with, but only a select few types are suitable for 3D printing (image courtesy of 3dhubs.com).
In order for a thermoplastic to be viable as a 3D printed material, it must fulfill 3 criteria:
1) The thermoplastic must be able to be extruded into plastic filament. In other words, it must be able to take the form of the 3D printing filament on the spools that you are probably familiar with.
2) It must be able to bind to the build plate and to itself in the 3D printing process while giving a smooth and accurate result.
3) It must be appropriate as a material choice for the end use application of the 3D printed part. The properties of the material should fit with its intended application (whether it needs to be strong, durable, shiny, etc.).

PLA and ABS have similar qualities and are suitable for a number of different applications, but they also differ in methods of operation and chemical makeup.
PLA or Polylactic Acid is created from processing a number of plant products such as corn, potatoes, or sugar-beets. PLA is biodegradable and can be composted at commercial compost facilities (it will not biodegrade itself in your backyard). It is considered to be much more earth-friendly and is stronger and more rigid than ABS (image courtesy of NatureWorks). PLA isn't as popular for objects that need to withstand heat for an extended period of time as it has a lower melting point than ABS. Both PLA and ABS can be sanded and machined to reach the desired outcome of the user.

ABS or Acrylonitrile butadiene styrene is petroleum based, made from different polymers in a continuous mass polymerization process. ABS pellets before they are processed into filament strands are pictured on the right. ABS can be engineered to have many properties, but it is in general a strong plastic with just a tad more flexibility than PLA. This slight flexibility makes ABS great for the creation of interlocking pieces, where PLA may be slightly more difficult to use. Furthermore, ABS is soluble in acetone, which can produce a shiny surface finish (pictured below, courtesy of wired.com). ABS has a higher temperature resistance than PLA but is also more difficult to work with due to the necessity of a heated print bed to bind the material as well as warping of the surface that is in direct contact with the heated bed. When printing ABS, the temperature of the surrounding air in the print chamber must be maintained so that it is not too cool and not too hot. Too much heat will lead to less accurate prints and more rounding of edges while too much cooling will lead to trouble in adhesion, resulting in cracks in the final product.

PLA on the other hand does not have as many requirements as ABS does to achieve a successful print. PLA is printed without a heated bed or a constant temperature chamber. Because PLA undergoes more of a phase-change than ABS (it becomes more fluid when heated), it can be actively cooled to produce more detailed prints without risks of cracking or warping. This also means that PLA has stronger binding between layers, resulting in an overall stronger part.
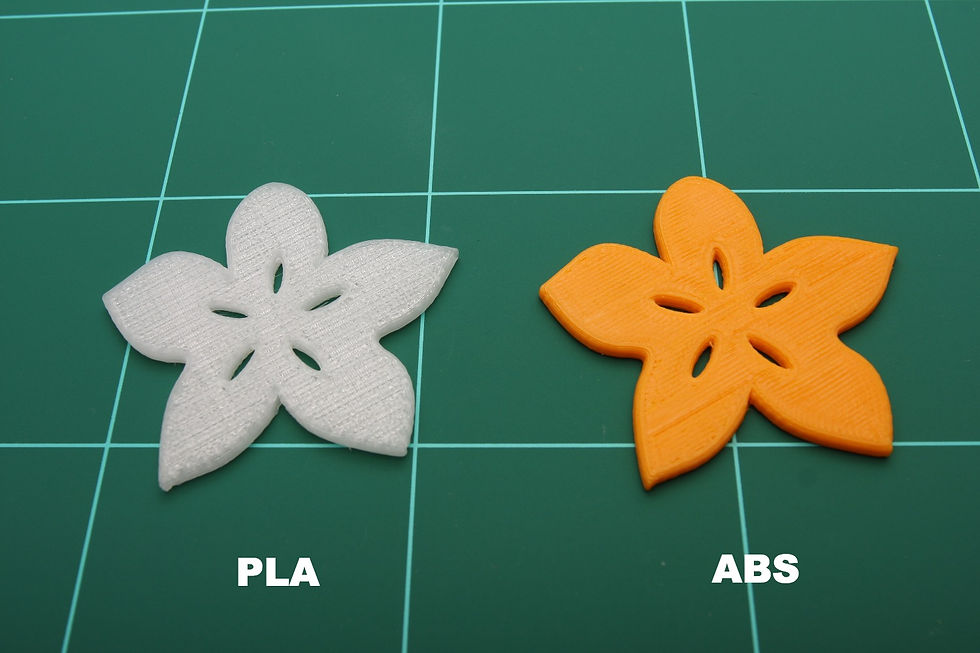
Off-gassing from a 3D printer can also be a health concern for many users. When melted, ABS gives off a strong smell of melting plastic. The particles that are emitted into the air have been found to be carcinogenic so proper ventilation is required in any room that printers will be operated in. Since PLA is created from plant-based materials, the smell given off is much less noticeable and can be likened with the smell of cooking oil. PLA particles are also less of a health hazard but good ventilation in printing areas is still advised as fewer long-term studies have been conducted on PLA.
Both PLA and ABS must be stored in a dry place, preferably in a ziplock bag containing a silica gel packet to maintain freshness. Humidity and moisture in the long term can have detrimental effects to print quality and operability in both materials.
PLA overall is more suitable for public use due to its ease of use, detail, and safety in health. It is popular in schools and libraries, and is recommended for beginning 3D printer users as well. ABS has been around longer and is used mostly in industrial settings or by those with more 3D printing experience who need its properties for a specific application.
Comments