A Brief History of 3D Printing
- Maryanne Olson
- Sep 13, 2016
- 3 min read
Although 3D printing only recently became a mainstream topic, its roots trace back to the 80's when Hideo Kodama of Nagoya Municipal Industrial Research Institute published the first account of a working photopolymer rapid prototyping system (1981). Shortly after this, the first form of 3D printing, Stereolithography, was invented by Charles Hull in 1984 (pictured above, image courtesy of industryweek.com). In stereolithography, a digital model can be created from pictures (see the process in the diagram below). This was a huge step forward for engineering and would make waves for inventors. With this invention, users could now test out designs and prototypes more efficiently before investing in large manufacturing batches. Charles Hull went on to found 3D Systems in 1986 which is currently one of the largest 3D printing companies alive today.
*diagram courtesy of solidsmack.com
In 1992 the first Stereolithographic Apparatus (or SLA machine) was produced by 3D Systems
(learn more about SLA printing HERE). The first SLA machine utilized a UV laser solidifying photopolymer, a liquid with the viscosity and color of honey that made objects layer by layer. This was the first form of rapid prototyping that would forever change the world of engineering and design. A modern-day SLA device is pictured on the right.
At around the same time, another form of additive manufacturing was in the works, called Selective Laser Sintering or SLS. In SLS, material in powder form is heated by a strong laser at just below its melting point, causing the powders to sinter together to form the solid 3D object which was intended to be made. This technology patent was filed in 1989 and was later licensed to a company called DTM Inc, which was later acquired by 3D Systems. The SLS process is depicted in the diagram below.

*diagram courtesy of mindtribe.com
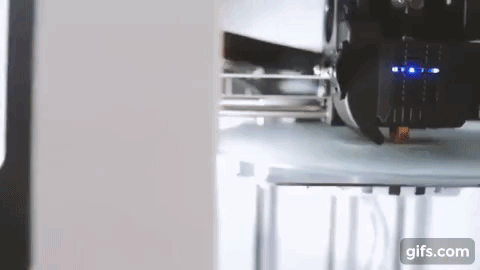
1989 was also the year that FDM printing (Fused Deposition Modeling; read more HERE) was patented by the co-founder of Stratasys, 3D System's competitor company. FDM is a proprietary technology still held by Stratasys today, but is also the process used by the majority of consumer machines (based on the open source RepRap model, pictured below).


Throughout the 90's and 2000's many new technologies continued to be introduced, still focused wholly on industrial applications meanwhile research and development was underway for more specific tooling, casting, and manufacturing processes. It was during this time that the term "Rapid Prototyping" was coined. Scientists were even beginning to create 3D printed organs for transplant using a patient's own cells and thus minimizing risk for rejection (a 3-dimensional bioprinter developed by the Russian company, 3D Bioprinting Solutions is pictured on the left).
3D printing began to diversify into 2 major sectors. The first was the high end, very expensive 3D printing equipment used in part production for high value, highly engineered, complex parts. Some industries that have seen great benefits from these technologies are the aerospace, automotive, medical and fine jewelry sectors.
The second sector comprises the 3d technologies whose aim was to improve concept development and functional prototyping. They were being developed as wallet-friendly systems that were user-friendly and could be operated in a non-industrial setting. This sector is where today's desktop 3D printers emerged from.
Throughout the 2000's 3D printing technology continued to evolve to include lower-priced models with different features. 2007 was an important year for the birth of accessible desktop 3D printers as the RepRap concept of an open source printer emerged but it wasn't until 2009 that the very first kit printer was available.
Since then, many more entry-level 3D printer manufacturers have emerged with lower prices and better accuracy. This brings us to present-day, where even students as young as elementary school are now learning product development with 3D printing technology. A desktop 3D printer is now commonplace among educational institutions and is a necessity in any engineer's office. AIO Robotics has further revolutionized 3D printing by creating the first standalone All-In-One system, ZEUS, complete with all 3D printing and scanning software fully built-in from the slicer to the on-board model editor and much more. Fully automated calibration and arguably the most user-friendly, intuitive interface makes the learning process for 3D printing simple for users of all ages. ZEUS enables even those that are not familiar with the technology to experience 3D printing by making the process as it should be, easy.

Having this technology accessible to so many has transformed the nature of inventing, making it painless and accessible for many more people to get their ideas out into the world. 3D printing has been touted as an industrial revolution in itself and we are honored to be a part of it. We can't wait to see what this game-changing technology will lead people to create next.
コメント